- Ferromagnetic materials can only be clamped using magnetism. Most steels are ferromagnetic and have good magnetic properties. Wood, glass, aluminium, and brass are not magnetic.
- A component is part of the magnetic circuit between the north and south poles of the magnet. The component must close the circuit as best as possible.
- Magnetic chucks have various types of pole orientation; see the figures below with the correct position of the workpiece.
SQUARE CHUCKS
Location of workpieces on square chucks
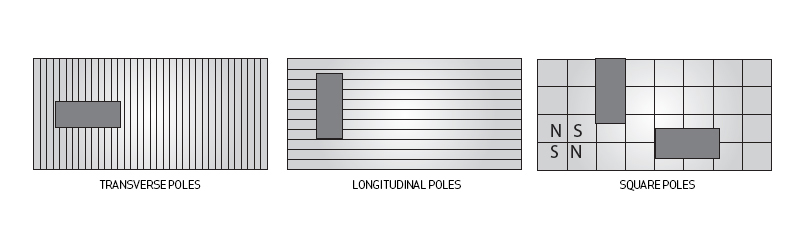
CIRCULAR CHUCKS
Location of workpieces on circular chucks
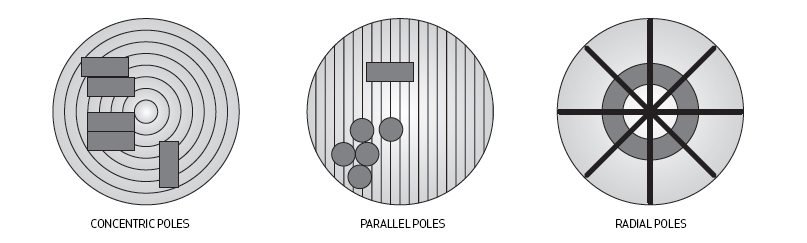
HOLDING FORCE
Fp is the holding force of magnetic chucks. This force is often specified as the “nominal” clamping force or the clamping force in dan/cm2 or kgf/cm2.
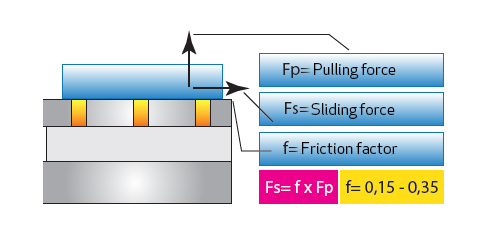
Nominal holding force is based on the standard testing method:
- Workpiece 50 x 50 x 20 mm in size
- Soft, low-carbon steel, e.g. S235JR
- Bottom contact surface
- Ambient temperature 20-25 °C
JIS standard: Contact area of the test piece is 1 cm2. This leads to a very high holding force per cm2.
FACTORS AFFECTING THE HOLDING FORCE
1. Contact area and surface condition – air gap
The closer contact between the element and the clamping area, the stronger the force. Weak contact, roughness, irregularities, abrasions, dirt, etc., create an air gap, which reduces the efficiency of the magnetic field.
2. Element thickness
The maximum holding force is only reached if the element is capable of conducting all available magnetic flux from the magnet pole. If the workpiece thickness is smaller than 50 % of the pole width, the holding force will be weaker.
3. Composition and material condition
Soft, low-carbon steel like S235JR has very good magnetic properties and it is an ideal material in terms of magnetism. Alloys and heat treatment reduce the magnetic properties and the maximum possible holding force. See Table.
4. Temperature
The nominal holding force is measured at room temperature, ranging from 20 °C to 25 °C. Higher temperatures, such as 60, 80 °C or more, affect the holding force due to the increased resistance in the magnetic circuit. The reduction of the holding force for permanent magnetic chucks is approximately 3% per every temperature increase by one degree Celsius.
DIN marking |
DIN marking |
Max. content of nonmag. alloy |
Heat treatment |
Magnetic Force |
Pure iron |
- |
0,00% |
Moderate |
105% |
Structural steel |
St37-2 |
1,0037 |
- |
Moderate |
100% |
St52-3 N |
1,0570 |
- |
Moderate |
98% |
St50-2 |
1,0050 |
- |
Moderate |
79% |
Hardened steel |
C10 |
1,0301 |
1,22% |
Moderate |
98% |
|
|
|
Hardened steel |
50% |
C15 |
1,0501 |
1,27% |
Moderate |
98% |
|
|
|
Hardened steel |
50% |
17CrNiMo6 |
1,87 |
5,43% |
Moderate |
76% |
|
|
|
Hardened steel |
40% |
16MnCr5 |
1,31 |
3,06% |
Moderate |
87% |
|
|
|
Hardened steel |
45% |
|
|
|
Moderate |
86% |
|
|
|
Hardened steel |
44% |
Nitrided steel |
34CrAl6 |
1,04 |
4,29% |
Untreated |
81% |
|
|
|
Nitrided |
53% |
31CrMoV9 |
1,19 |
4,65% |
Untreated |
80% |
|
|
|
Nitrided |
51% |
34CrAlNi7 |
1,50 |
5,93% |
Untreated |
74% |
|
|
|
Nitrided |
48% |
39CrMoV13-9 |
1,23 |
6.44% |
Untreated |
71% |
|
|
|
Nitrided |
46% |
Free-cutting steel |
15S10 |
1,0710 |
1,77% |
Untreated |
95% |
9SMn28 |
1,0715 |
1,92% |
Untreated |
94% |
45S20 |
1,0727 |
2,21% |
Untreated |
93% |
60Pb20 |
1,0758 |
2,71% |
Untreated |
89% |
Heat-treated steel |
C22 |
1,0402 |
2,96% |
Moderate |
88% |
|
|
|
Tempered |
51% |
C45 |
1,0503 |
3,20% |
Moderate |
85% |
|
|
|
Tempered |
50% |
Ck45 |
1,1191 |
3,50% |
Moderate |
85% |
|
|
|
Tempered |
50% |
C60 |
1,0601 |
3,57% |
Moderate |
85% |
|
|
|
Tempered |
49% |
Ck60 |
1,1221 |
3,65% |
Moderate |
84% |
|
|
|
Tempered |
49% |
43CrMo4 |
1,63 |
3,62% |
Moderated |
84% |
|
|
|
Tempered |
49% |
36CrNiMo4 |
1,11 |
4,37% |
Moderate |
81% |
|
|
|
Tempered |
47% |
Roller bearing steel |
100Cr6 |
1,01 |
3,11% |
Moderate |
87% |
|
|
|
Hardened steel |
45% |
100CrMn6 |
1,20 |
5,26% |
Moderate |
77% |
|
|
|
Hardened steel |
40% |
C102CrMo17 |
1,43 |
22,72% |
Moderate |
27% |
|
|
|
Hardened steel |
14% |
X8WMoCrV6-5-4 |
1,53 |
11,40% |
Moderate |
46% |
|
|
|
Hardened steel |
25% |
Spring steel |
Ck67 |
1,1231 |
2,04% |
Moderate |
93% |
|
|
|
Hardened steel |
48% |
60SiMn5 |
1,42 |
3,15% |
Moderate |
87% |
|
|
|
Hardened steel |
45% |
51MnV7 |
1,25 |
2,87% |
Moderate |
88% |
|
|
|
Hardened steel |
46% |
Cold extrusion steel |
Cp15 |
1,1132 |
1,10% |
Moderate |
99% |
41Cr4 |
1,35 |
3,55% |
Moderate |
85% |
OPTIMISATION OF THE HOLDING FORCE
- Air gap reduction: Remove burrs, lumps, rust, and scale. If necessary, clean the element. If the element comes loose, use magnetic adapters.
- If the workpiece has small dimensions, extend or combine the magnetic circuit by creating groups of small elements, thereby allowing the magnetic flux to rest against a larger area.
- For large elements, use extensions to avoid overturning or tilting during machining.
- Use stop bars to secure the workpiece against displacement.
- Use pole extensions for components with irregular shapes.